News & Events
Resources
Downloads
IrgaCycle® Flyer
Case Study: Multiple-Loop Polypropylene Recycling
Case Study: Avoiding Gel Formation in r-LDPE Recycled Film
Frequently Asked Questions
What is the difference between mechanical and chemical recycling?
The main difference between these two recycling approaches is the impact to the polymer structure. Chemical recycling, which includes many different specific technologies, returns the polymer to its original building blocks (monomers), or even back to feedstock material in order to produce new plastics.
Mechanical recycling preserves the plastic molecular structure, utilizing less energy intensive processes to clean it, melt it, and reshape it for use as recycled plastic.
In both cases, recycling helps keep plastic waste out of the environment and reduces the need to produce new plastics.
What are the main challenges of mechanical recycling?
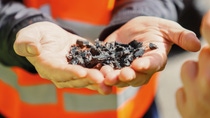
Many challenges exist throughout the mechanical recycling value chain illustrated above, starting with the availability and execution of a collection infrastructure. For example, only about 15% of plastic waste is collected in the US, but in Japan and Germany, the number is 87% and 67% respectively due to smaller geographic distances and extensive investment in waste collection infrastructure.
Once material has been collected, it is necessary to sort the plastic. In some places around the world, this sorting is done by hand, while in other locations advanced sorting robots and sensors are used to separate plastic types from each other and from other materials in the recycling stream. Sorting is important step in the process, as many plastic types can not be mixed or the resulting recycled material will not be suitable for reuse.
Cleaning the sorted plastics presents the next challenge: is it possible to remove all pollution, labels, and residues? The answer is YES, but it’s certainly not easy. Complex packaging design means that multiple layers might need to be separated, inks and adhesives must be removed, and any other contaminants must be washed away.
Finally, the sorted, cleaned plastic must be reprocessed. Heating plastics to melt and reform them also leads to degradation of the polymer itself. Not knowing exactly where the plastics come from means that there are also variations in the quality and age of the material. These variations can lead to poor processing of the material and result in low quality, low performance PCR. Additional chemical stabilizers can help reduce these issues but require testing to optimize the best solution.
Successfully recycling plastics into high quality applications at large scale requires collaboration at each point of the value chain.
Is mechanical recycling really beneficial for the environment?
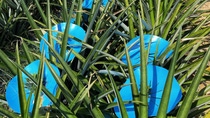
Simply increasing the amount of plastic that are recycled immediately reduces the amount of waste that is sent to landfills or leaks into the environment. That alone should be enough motivation to increase recycling globally.
On top of that, mechanical recycling plastics reduces the need to extract more natural resources to produce new plastics. The U.S. EPA calculates that recycling just 1 plastic bottle can save enough energy to power a laptop for 2.5 hours!!
The data is still being generated, but mechanical recycling is also considered to have lower CO2 emissions than other recycling technologies, and certainly less than the creation of new plastic articles.
Sources:
Recycling in the United States | US EPA
National Overview: Facts and Figures on Materials, Wastes and Recycling | US EPA
Can all plastics be recycled?
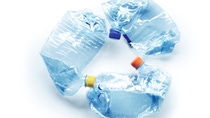
Most plastics can be recycled! Many pieces of plastic, particularly packaging items, are marked with Resin Identification Codes (RIC) that indicate the type of plastic used to make the item. However, not all recycling facilities can recycled each type of plastic, as they can require very different treatment processes.
The most commonly recycled plastics include polyethylene terephthalate (PET), High-Density Polyethylene (HDPE), Low-Density Polyethylene (LDPE), and Polypropylene (PP) correlated to RIC #1, #2, #4, and #5. Each of these materials can be well sorted, cleaned, and enhanced with additives to produce high quality recycled plastics.
Other plastic types may require specialized mechanical recycling steps and may be better considered for other recycling technologies.
Always check with your local recycling organizations to learn what types and shapes of plastics can be recycled in your area.
Source: Check Locally - How2Recycle